Introduction
The frequency of servicing for a cargo lift depends on several factors, including the lift’s usage, environmental conditions, manufacturer’s recommendations, and regulatory requirements. While there is no one-size-fits-all answer, here are some general guidelines for servicing a cargo lift:
Different Makes & Models
The frequency of servicing is also dependent on the make and model of the lift. So its best to refer to the manufacturer’s recommendation when determining the frequency of servicing for a cargo lift. The lift owner can refer to the manufacturer’s guidelines and maintenance schedule outlined in the lift’s operation manual. Manufacturers often provide recommendations for routine maintenance tasks, including the frequency of servicing based on hours of operation or specific intervals.
Usage Patterns
Consider the frequency and intensity of cargo lift usage. If the lift operates continuously or experiences heavy usage, more frequent servicing may be required to ensure optimal performance and safety. Conversely, if the lift is used infrequently, servicing intervals may be less frequent.
Environmental Conditions:
Environmental factors such as humidity, temperature fluctuations, dust, and corrosive substances can affect the condition of lift components. Lifts installed in harsh environments may require more frequent servicing to mitigate the impact of environmental factors on mechanical and electrical systems.
Regulatory Requirements:
Regulatory authorities may stipulate specific maintenance intervals or inspection requirements to ensure compliance with safety standards.
Condition Monitoring:
Implement condition monitoring techniques such as visual inspections, performance testing, and remote monitoring to assess the health of the cargo lift system. Regularly monitor key performance metrics and address any abnormalities or signs of wear promptly to prevent breakdowns and ensure safety.
Risk Assessment:
Conduct periodic risk assessments to identify potential safety hazards and prioritize maintenance tasks accordingly. Factors such as the age of the lift, past maintenance history, and the criticality of lift operations should be considered when determining servicing intervals.
Professional Consultation:
Consult qualified lift maintenance professionals or service providers to assess the specific requirements of your cargo lift system. Experienced technicians can provide insights into best practices for maintenance and servicing based on the unique characteristics of your lift installation.
Conclusion:
In summary, the frequency of servicing for a cargo lift should be determined based on a combination of manufacturer recommendations, usage patterns, environmental conditions, regulatory requirements, condition monitoring, risk assessment, and professional consultation. By implementing a proactive maintenance strategy tailored to the specific needs of the cargo lift system, building owners can ensure its reliable operation, minimize downtime, and prioritize safety for users and cargo alike.
At KH Lift & Elevator, we offer a comprehensive maintenance package that can be customised to suit your needs. If you are also interested to find out more or how KH Lift & Elevator’s RM&D service can help you to reduce costs and maintain your lift safely and efficiently, contact us for a complimentary consultation.
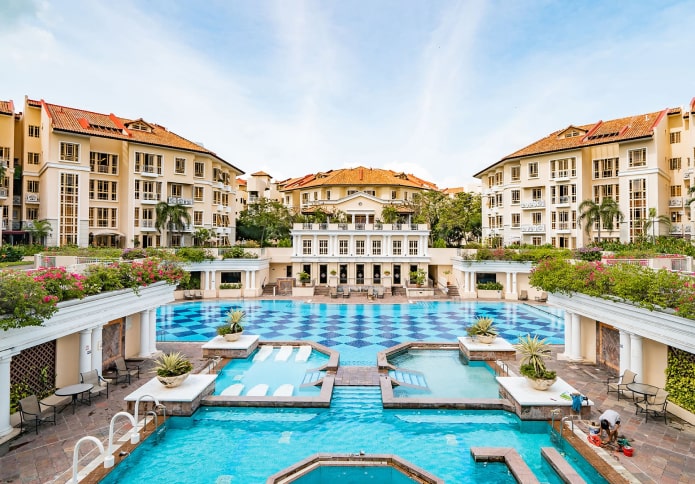
Browse Our Projects
With 27 years of experience to our belt, check out our list of lift servicing projects or products below.