Introduction
In our urban Singapore, lifts play a very big role in our daily lives and operation. To ensure the uninterrupted operation and safety of lifts, a well-crafted maintenance plan is indispensable. In this article, we’ll explore the key components of a comprehensive lift maintenance plan and how it contributes to the efficient functioning and longevity of lift systems.
Note: This lift maintenance plan serves as a guideline and may be customized based on specific requirements and conditions of the lift system and property. A good lift maintenance plan provides a structured framework for ensuring the safe, reliable and efficient operation of lift systems.
Lift Maintenance Plan
The lift maintenance plan typically begins with the following informations:
Property Name/Address: [Insert Property Name/Address]
Lift Manufacturer: [Insert Lift Manufacturer]
Lift Model/Type: [Insert Lift Model/Type]
Maintenance Provider: [Insert Maintenance Provider]
Contract Start Date: [Insert Start Date]
Contract End Date: [Insert End Date]
And consist of an overview section that outlines the scheduled maintenance activities and protocols for ensuring the safe and efficient operation of the lift system installed at the mention property name and address.
Assessment and Evaluation:
The foundation of any effective lift maintenance plan begins with a thorough assessment and evaluation of the existing lift system. This includes a comprehensive inspection of all lift components, from the mechanical and electrical systems to the structural integrity of the lift shaft. By conducting a detailed assessment, maintenance professionals can identify potential issues, assess the condition of critical components, and determine the overall health of the lift system.
Assessment and Evaluation:
The foundation of any effective lift maintenance plan begins with a thorough assessment and evaluation of the existing lift system. This includes a comprehensive inspection of all lift components, from the mechanical and electrical systems to the structural integrity of the lift shaft. By conducting a detailed assessment, maintenance professionals can identify potential issues, assess the condition of critical components, and determine the overall health of the lift system.
Establishing Maintenance Schedule:
Based on the findings of the assessment, a maintenance schedule should be established to ensure regular inspections and preventive maintenance tasks are carried out at appropriate intervals. The frequency of maintenance activities may vary depending on factors such as lift usage, environmental conditions, and regulatory requirements. A well-defined maintenance schedule ensures that critical components are inspected and serviced on a regular basis, minimizing the risk of unexpected breakdowns and ensuring the safety of passengers.
The maintenance schedule outlines the frequency and scope of maintenance activities to be conducted on the lift system:
Monthly Inspections: Conduct visual inspections, lubricate moving parts, and check for any signs of wear or damage.
Quarterly Servicing: Perform comprehensive inspections, test safety features, and conduct preventive maintenance tasks such as adjustment of tension mechanisms and calibration of control systems.
Semi-Annual Maintenance: Conduct thorough examinations of critical components, including cables, pulleys, brakes, and electrical systems. Replace worn-out parts as necessary.
Annual Maintenance: Conduct in-depth servicing, including hydraulic fluid analysis (if applicable), and perform any necessary upgrades or modernization tasks.
You may also refer to this guide to read on how often a lift maintenance is required.
Routine Inspections and Preventive Maintenance:
Routine inspections and preventive maintenance are essential components of a lift maintenance plan. Trained technicians should conduct regular inspections of all lift components, including cables, pulleys, brakes, and electrical systems, to identify potential issues before they escalate. Preventive maintenance tasks such as lubrication of moving parts, adjustment of tension mechanisms, and calibration of control systems should be carried out as per the established schedule to ensure optimal performance and longevity of lift components.
Refer to this checklist sample for your lift maintenance plan.
Compliance with Regulatory Standards:
Compliance with regulatory standards and safety requirements is paramount in lift maintenance. A comprehensive maintenance plan should ensure that all maintenance activities are carried out in accordance with relevant building codes, occupational health and safety regulations, and industry standards. Regular inspections and certifications conducted by accredited professionals help ensure that the lift system meets all safety requirements and operates in compliance with regulatory standards.
Emergency Response Plan:
Despite proactive maintenance measures, emergencies may still arise. A well-crafted lift maintenance plan should include provisions for emergency response, including a designated emergency contact, 24/7 availability of trained technicians, and a clear protocol for responding to lift breakdowns, entrapments, or safety hazards. A swift and efficient response to emergencies is essential for minimizing downtime, restoring lift service, and ensuring the safety of passengers.
Data-Driven Monitoring and Analysis:
Incorporating data-driven monitoring and analysis tools into the maintenance plan can provide valuable insights into the performance and health of the lift system. Advanced technologies such as Remote Monitoring and Diagnostics (RM&D) utilize sensors and analytics to track key performance metrics, detect anomalies, and predict potential issues before they impact lift operation. Real-time monitoring allows maintenance professionals to identify trends, optimize maintenance schedules, and make data-driven decisions to enhance lift performance and reliability.
Continuous Improvement and Adaptation:
A lift maintenance plan should not be static but rather evolve and adapt over time based on changing conditions and emerging technologies. Continuous improvement initiatives, such as regular reviews of maintenance procedures, incorporating feedback from maintenance technicians and building occupants, and staying abreast of industry advancements, help ensure that the maintenance plan remains effective and responsive to evolving needs and challenges.
Documentation and Reporting:
Maintain comprehensive records of all maintenance activities, including inspection reports, service logs, and certification documents. Provide regular updates and reports to the property management team to ensure transparency and accountability.
Contract Terms and Renewal:
Review contract terms, including duration, scope of services, and pricing, and ensure timely renewal to maintain uninterrupted service provision.
Conclusion:
A well-crafted lift maintenance plan is essential for ensuring the reliable operation, safety, and longevity of lift systems. By incorporating assessment and evaluation, establishing a maintenance schedule, conducting routine inspections and preventive maintenance, ensuring compliance with regulatory standards, implementing an emergency response plan, leveraging data-driven monitoring and analysis, and fostering a culture of continuous improvement, maintenance professionals can optimize lift performance, minimize downtime, and ensure the safety and satisfaction of building occupants. With a proactive and comprehensive maintenance plan in place, lifts can continue to ascend safely and efficiently, playing a vital role in the seamless functioning of modern buildings and urban environments.
At KH Lift & Elevator, we offer a comprehensive maintenance package that can be customised to suit your needs. If you are interested to find out more or how KH Lift & Elevator’s RM&D service can help you to reduce costs and maintain your lift safely and efficiently, contact us for a complimentary demo consultation.
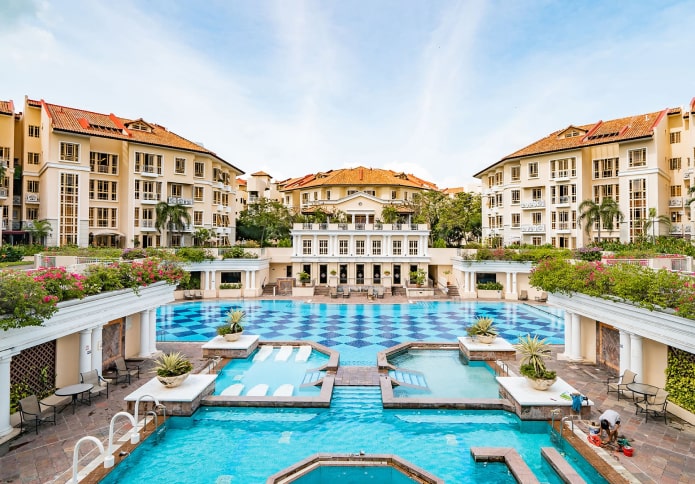
Browse Our Projects
With 27 years of experience to our belt, check out our list of lift servicing projects or products below.